Extrusion via self-lubricated photopolymerization for manufacturing and self-growing robots
A self-lubricated photopolymerization extrusion method for continuous production of profiled polymer parts, which can be deployed in self-growing robots capable of executing a range of tasks, including exploration, burrowing, and traversing tortuous paths.
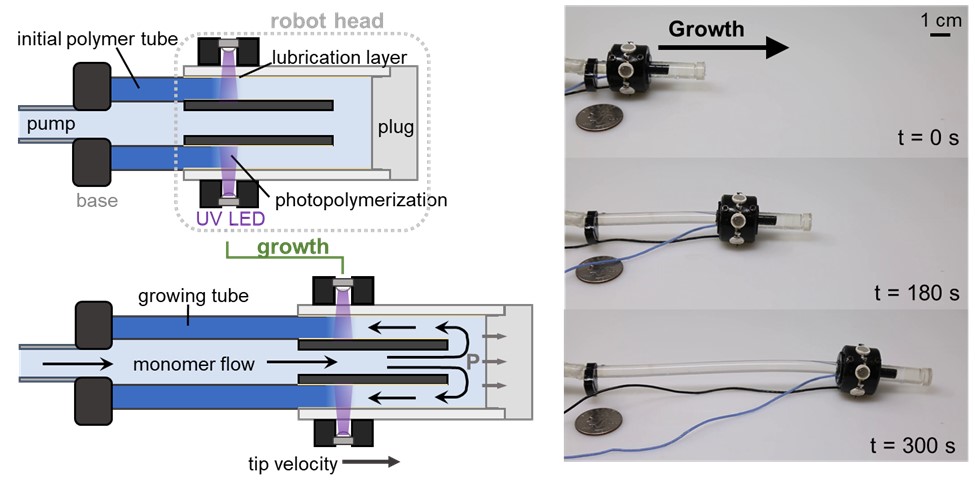
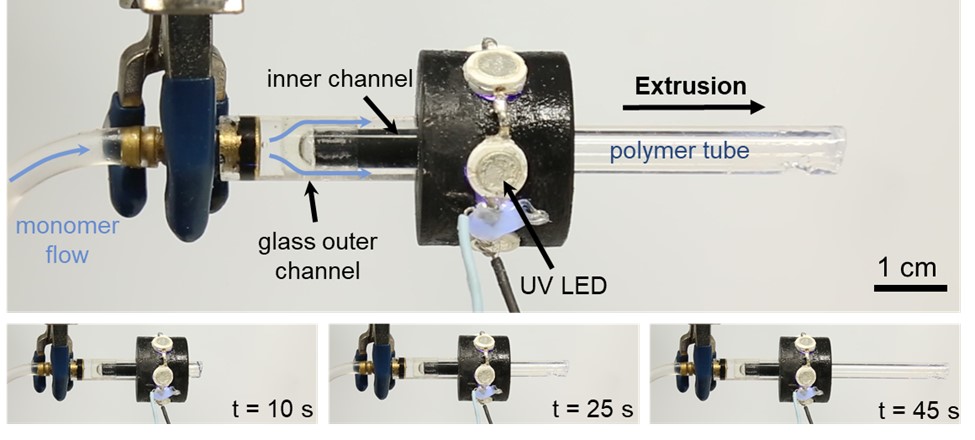
Applications
- General parts manufacturing through self-lubricated extrusion
- Catheters/medical devices within the human body
- Inspection of hard to access spaces such as broken/leaky pipes
- Burrowing for subterranean generation of tubing and piping
- Construction robots for installation of tubing or beams to build structures
- Installation of infrastructure such as irrigation or wiring
- General exploration in unusual/remote environments (space, deep sea, caves, archaeological digs)
Key Benefits & Differentiators
- Continuous extrusion of profiled parts: by using block copolymers to form a self-lubricating layer that minimizes friction and adhesion of polymers onto the channel surfaces.
- Profiled parts with tunable properties: capable of producing solid profiled parts with abrupt or tapered mechanical properties by adjustments in photochemistry
- Easy manufacturing: the process does not require extruders or heating and can be operated at significantly lower pressures
- Manufacturing of self-growing robots with unrestricted growth: by using liquid material (monomers) to generate the growing body of the robots, this method eliminates the internal friction that eventually prohibits growth in other robots
- Self-growing robots with enhanced capabilities: photopolymerization permits significant control over material properties as the body grows, which can be used to adjust stiffness, robot steering, and to avoid obstacles
Technology Overview
Continuous manufacturing of solid profiled polymer parts is challenging because common polymers have strong adhesion to various surfaces such as metal, glass, and other polymers. This leads to increased friction and eventually failure of the manufacturing process. Current available techniques to manufacture high-aspect profiled polymer parts are severely limited, and often require high melting temperatures, high-pressures, and complex machinery. Newly developed 3D printing techniques such stereolithography or vat photopolymerization can convert a liquid resin into solid parts via photopolymerization. However, they have limited applicability due to their finite build volumes and relatively low throughput. To address this limitation, Researchers at the University of Minnesota have developed a self-lubricated photopolymerization method that is able to continuously convert monomer fluid into a solid part. This novel method can be used to manufacture crosslinked polymer parts from various starting materials such as various meth(acrylate) monomers, but could also be readily extended to other photopolymerizable monomers. For instance, this novel photopolymerization technique can be used to produce growing robots with enhanced capabilities.
Growing robots are inspired by the biological tip growing process through which plant roots and vines are able to direct growth to reach new locations. As such, these robots interact with the environment by growing at their tip, instead of moving through surface contact like traditional robots. Unfortunately, current robots mostly grow using solid-state materials, which severely limits lengthening and their navigation capabilities. The novel self-lubricating photopolymerization technique addresses these problems by eliminating internal friction, which in turn allows for unrestricted growth of the robot's body through the environment. In addition, photopolymerization enables control over the material properties and growth patterns at the tip, which ultimately facilitates bending of its parts, navigation, and steering to avoid obstacles. Therefore, a growing robot utilizing the proposed method is capable of lengthening many times its original body length, burrowing in a simulated soil, passively avoiding obstacles, and traversing tortuous paths. A greater range of functionalities, including biodegradability, improved mechanical properties, and active steering, could be achieved by employing different chemistries and robot designs.
Phase of Development
TRL: 3-6Working prototype demonstrating both the extrusion process and a growing soft robot with different behaviors such as growth, passive steering, and burrowing is available.
Desired Partnerships
This technology is now available for:- License
- Sponsored research
- Co-development
Please contact our office to share your business’ needs and learn more.
Press Releases
Researchers
- Christopher Ellison, PhD Professor, Department of Chemical Engineering and Materials Science
- Tim Kowalewski, PhD Associate Professor, Mechanical Engineering Department
- Lorraine Francis, PhD Professor, Department of Chemical Engineering and Materials Science
-
expand_more library_books References (1)
- Hausladen, Matthew M,Zhao, Boran,Kubala, Matthew S.,Francis, Lorraine F.,Kowalewski, Timothy M.,Ellison, Christopher J. (2022), Synthetic growth by self-lubricated photopolymerization and extrusion inspired by plants and fungi, Proceedings of the national academy of sciences
-
expand_more cloud_download Supporting documents (1)Product brochureExtrusion via self-lubricated photopolymerization for manufacturing and self-growing robots.pdf