A novel Vertical Axis Wind Turbine (VAWT)
A novel Vertical Axis Wind Turbine well-suited for urban, suburban, and exurban areas
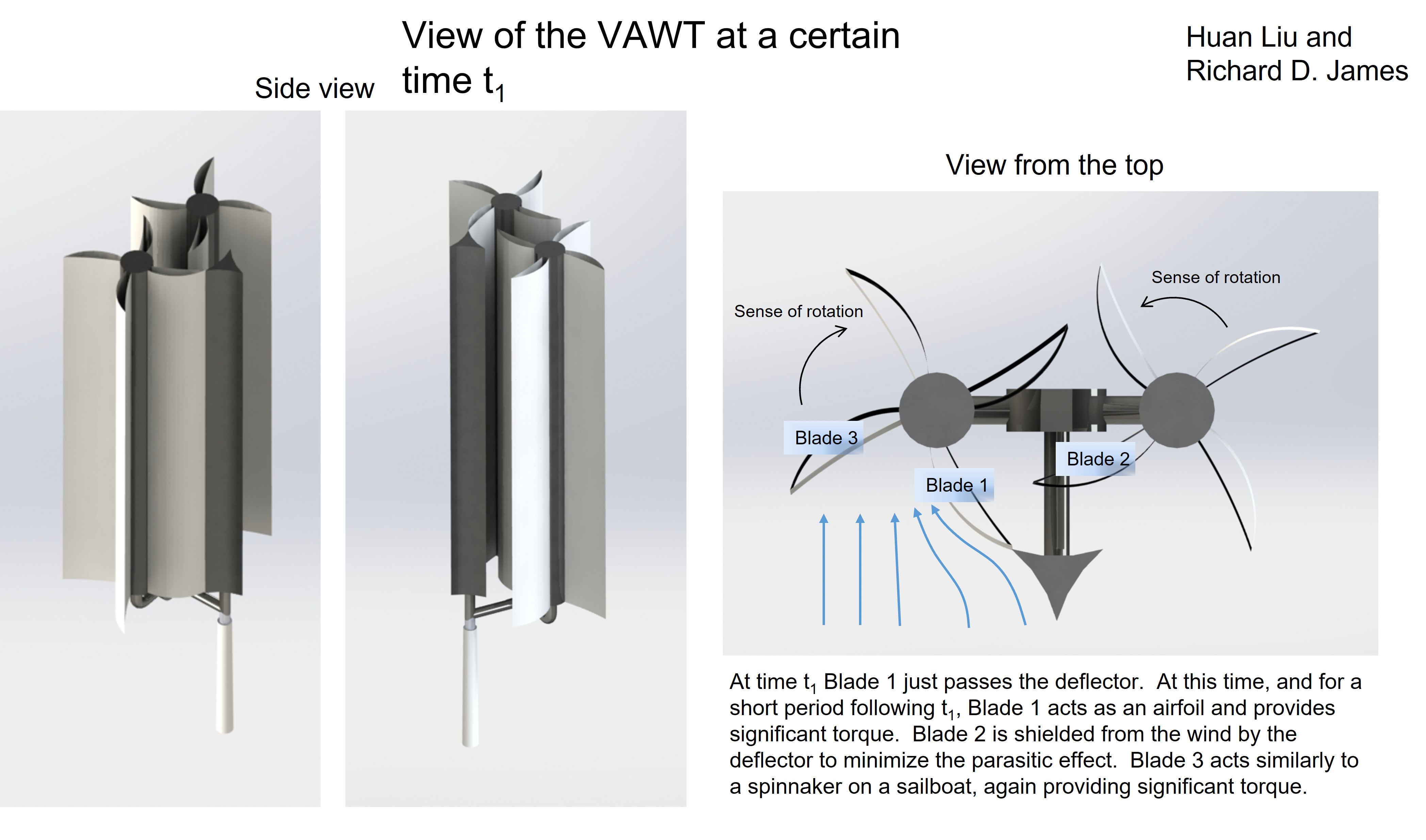
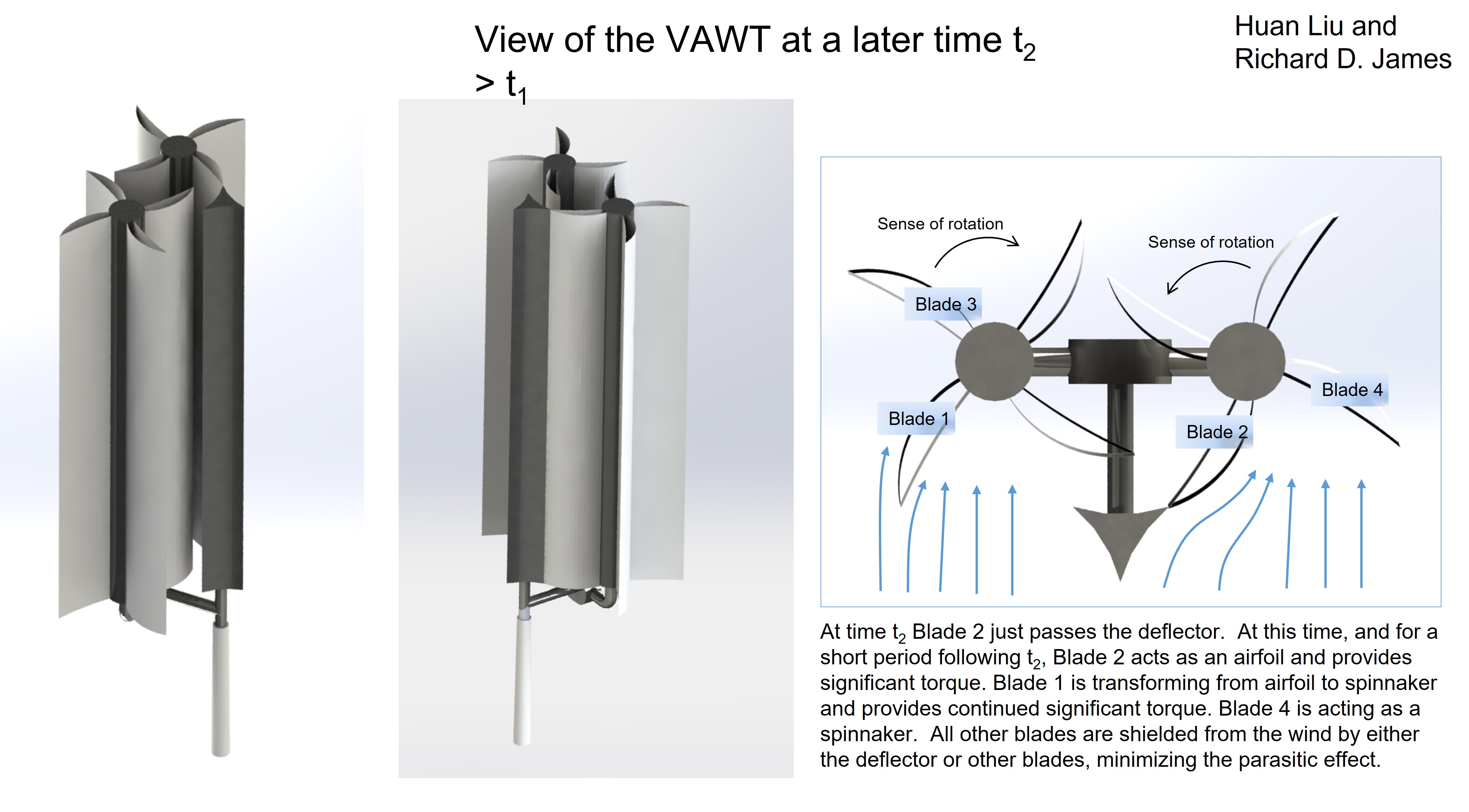
Applications
- Wind Energy
Key Benefits & Differentiators
- Enhanced power output: Due to the architecture of the rotors and a deflector which promotes increased wind loading.
- Lower physical/spatial footprint: Owing to the vertical axis architecture.
- Lower installation and maintenance costs: Due to simpler design.
- Easier to transport and implement in densely populated areas: Due to smaller size, simple modular design, accessibility of generator and moving parts at the base.
Technology Overview
Harnessing power from the wind via wind turbines is one of the cleanest and most sustainable ways to generate electricity. There is not yet a widely deployed vertical axis wind turbine, although it potentially can exhibit benefits such as simple design, low spatial footprint, and easy maintenance due to the fact that the generator is at the base which also lowers the risk for birds. The challenges in current vertical-axis wind turbines are mainly due to their inefficiency in terms of the power output vs. wind speed for a given height and diameter. This inefficiency is overcome by use of modern aerodynamic design principles and structural origami design methods.
Researchers at the University of Minnesota have developed a novel design for a Vertical Axis Wind Turbine (VAWT), which would provide enhanced power output in addition to other advantages. The VAWT design includes a stage and a deflector. The stage includes two turbine sub-units, each with a rotor, and the rotor blades intermesh during rotation. The deflector diverts the incident wind away from the parasitic side of the blades which enhances wind loading leading to increased power output. Due to the vertical axis aspect and the simple nature of the design, this would be ideal for urban, suburban, and exurban areas where a lower spatial footprint is key. Additionally, transportation of this wind turbine would be easier since this would entail fewer moving parts (e.g. no gearbox).
Phase of Development
TRL: 3-4At a concept stage with simulations being performed. The next step is to develop a scaled prototype.
Desired Partnerships
This technology is now available for:- License
- Sponsored research
- Co-development
Please contact our office to share your business’ needs and learn more.
Researchers
- Richard D. James Professor, Department of Aerospace Engineering Mechanics